The new scene from Landman is met with cheers from one side and a large distrust of the facts stated from the other, leaving little between.
‘Please Mr. Oil Man, tell me how the wind is bad for the environment.’
‘400 feet tall, the concrete foundation covers a third of an acre and goes down 12 feet.’
Typical 400’ foot(122m) turbine today is a 3MW… and down the rabbit hole we go.
‘Do you have any idea how much diesel they have to burn to mix that much concrete?’
According to the U.S. Energy Information Administration (EIA), the cement industry is ‘the most energy-intensive of all manufacturing industries, with a share of national energy use roughly 10 times its share of the nation's gross output of goods and services’. With the EIA projecting the concrete industry will increase energy consumption in the long term.
Cement is foundational to modern society, figuratively and literally, made up of 10-15% limestone and clay heated to ~1450°C (71% limestone and combinations of 16% cement rock), 15-20% water, and 60-75% sand and crushed stone/gravel. The process includes mining the limestone and clay and crushing the raw materials to be processed with logistics to move the products to the processing plants and the mixing and pouring inputs required to achieve the final product. ‘The marginal cost of cement production is estimated at $130/ton… around 100kWh/ton of electricity use is the grinding of inputs and clinker.’
With a diameter of ~65 feet (18-20m) and an average depth of 12 feet (3.7m) calculated based on the Piled Concrete Foundation Model structure to support a 3-MW wind turbine. The total foundation has approximately 45 tons of steel with 5-6 tons from anchor and cage bolts to the bulk of the steel in the rebar and reinforcement steel coming in at ~35-40 tons.
‘Or mix that steel and haul this sh*t out here?’’
This requires 40-45 truckloads of concrete or ~400 cubic yards to be moved to location and poured by a crew. Each footing weighs about 2M pounds and remains in place even after the turbine is decommissioned. A study by the Department of Energy in 2024 found that of all the truck types, concrete mixers had the lowest average fuel economy at 4.0 mpg. There isn’t much about the production and laying of concrete that is environmentally friendly.
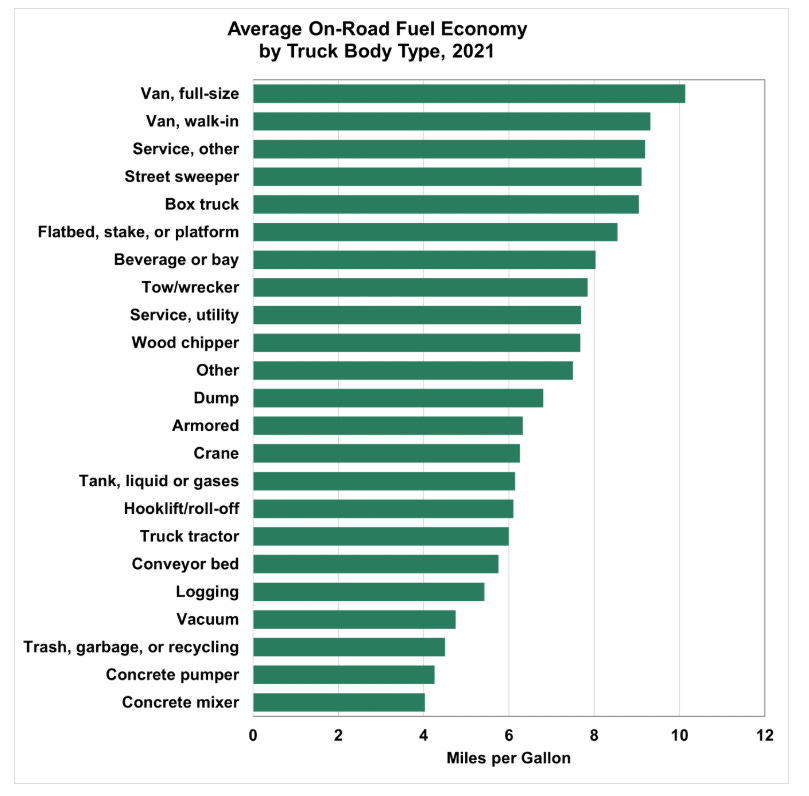
The location of wind turbines onshore is not equally distributed across the world or even the United States with location varying based on viability and the production of energy through the source of wind. In other words, you can’t put turbines where the wind doesn’t blow and too far from the needs due to transmission capacity. Below is a map of the current locations of onshore wind in the United States compared to population density.
A map showing the location of cement plants and counties producing construction sand and gravel and crushed stone (Data from the USGS) below. Transporation of raw inputs for producing the concrete stretch a wide geological distance.
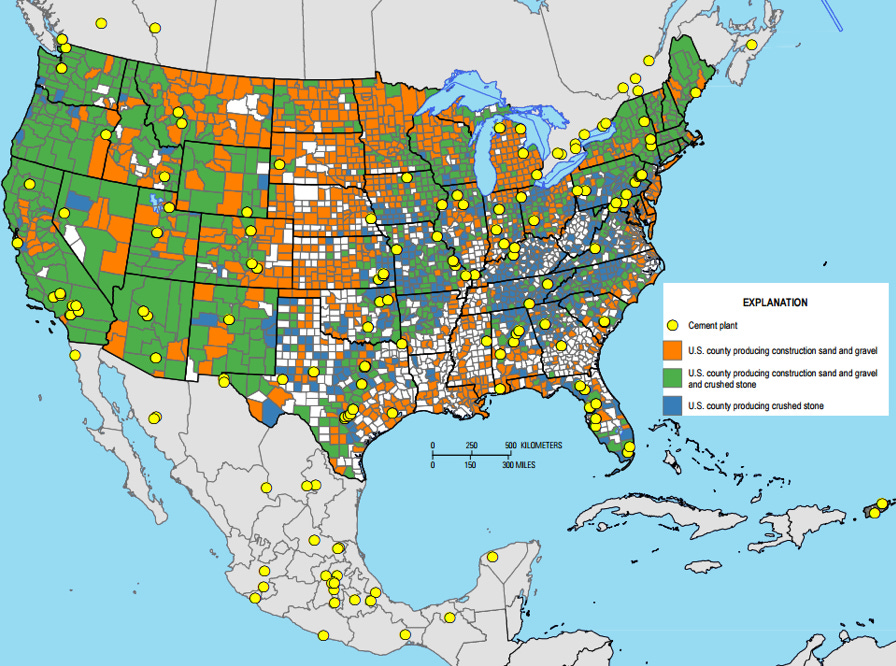
‘..put it together with a 450 foot crane’
The main tower consists of A572-50 (US standard) for main sections with a high tensile strength of 355-520 MPa to ensure structural integrity. The breakdown in tons is ~170-180 for the main tower, ~8-10 tons for the platform and internal ladder, ~5-6 tons of bolts/anchors in tower, ~35-40 tons of rebar, ~5-6 tons of bolts/anchors in foundation, ~22-25 tons for main frame, ~6-8 tons generator frame/housing, ~10-12 tons for gearbox, ~12-15 tons for the hub, ~6-8 tons for blade supports and pitch system, and ~20 tons for the total rotor bring it in at a total steel content of ~295-300 tons. This excludes the copper for cabling and generator, cast iron for the gear box assembly, and aluminum.
Approximately 500 kWh is needed to melt one metric ton of scrap steel in a modern electric arc furnace, for 300 tons(300 × 500-550 kWh) is 150,000-165,000 kWh. ‘It takes up to 3 kg (6.6 lb) of graphite electrodes to produce one ton of steel. This means that you can expect 900 pounds of graphite electrodes to be needed for your 150-ton batch of steel.’ according to FRC Global. Additional energy requirements include preheating, holding temperature, and mixing and alloying.
This comes out to an estimated total of nearly 200,000 kWh of energy needed to produce the entire steel needed for a single 3MW wind turbine. This does not include the energy inputs needed to weld and assemble the towers.
‘Wanna guess how much oil it takes to lubricate that fucking thing or winterize is?
Shell shows a long list of different parts within the wind turbines that require lubricants show in the table below:
Initial fill of the gear box requires 132-158 gallons and an annual top off of 13-21 gallons. While Shell claims the lifespan of their lubricants are 20+ years with Shell Omala S5 Wind 320, a complete change interval is usually every 3-5 years. Other components such as pitch system, main bearings, generator bearings, and yaw require 23-27 gallons of lubricants bring the total lubricants to 155-185 gallons with annual maintenance of 26-40 gallons or an additional 660 gallons on average over 20 years.
Anti-icing for blades can be achieved in a number of different ways including passive de-icing techniques using flexible blades designed to shed the ice by the blade bending shear force and blade pitching by turns blades to the sun to receive more heat energy. These methods are not fully sustainable without active anti-icing techniques that are required for heavier icing. One method of active is to heat the blades through electrical resistance to keep the blades above 0℃.
The ice doesn’t form symmetrically on the turbine blades, which can cause imbalance and potentially cause damage to the gearboxes. If the turbines are at a standstill for a longer period, damages can also be caused to the bearings. In extreme climates, a solution had to be developed to de-ice the turbines at a faster rate through active measures such as using a helicopter and hot water. In a study de-icing ten turbines at Uljabuouda, the round-trip Boden-Uljabuouda is 500 km anticipating it would take three days to de-ice ten turbines.
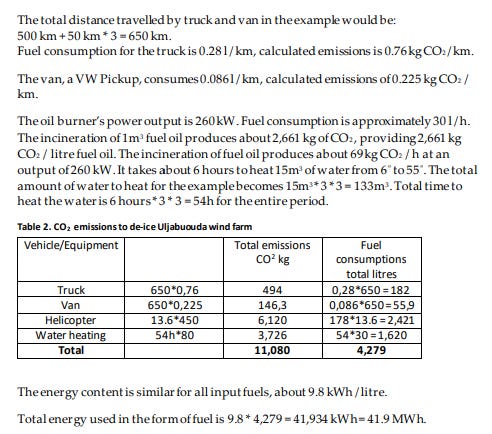
The results of the paper referenced above showed that ‘overall, it provides a release of about 1,100kg CO2 / turbine for the example above with ten turbines. De-icing should only be performed when there are high expectations for good wind access without the risk of icing.’
‘In its 20-year lifespan it won’t offset the carbon footprint of making it’
According to the U.S. Energy Information Administration (EIA), ‘wind turbines are designed with lifespans of between 20 and 25 years, wind capacity factors decline with age as mechanical parts degrade, according to the U.S. Department of Energy’s Wind Technologies Market Report. The United Kingdom’s Engineering and Physical Sciences Research Council in 2014 indicated that, on average, the output of wind turbines declines by 1.6% each year. ‘
Decommissioning of blades is at a faster rate than that of the total tower for each turbine with a waste expectation of 200,000 to 370,000 tons per year by 2050 where the operational lifespan of the blade is between 15-25 years. Wind turbine blades consist primarily of composite materials - a combination of glass and/or carbon fibers embedded in polymer matrices - making up 80-90% of their total weight. The remaining 10-20% includes steel components, protective paint coatings, balsa wood cores, bonding adhesives, internal cables, and various other materials.
The size of the blades and total tons per year will require innovations in recycling due to the landfill requirements to decommission such a large number of blades. With an estimated 60,000-85,000 utility-scale of onshore turbines by 2050
‘Don’t get me started on solar panels and the lithium in your Tesla battery’
Onshore wind is dominant for material input needs in alternative energy with a relatively high material use of 7.1 tons/GWh compared to nuclear energy is about 0.6 to 1.4 tons/GWh.
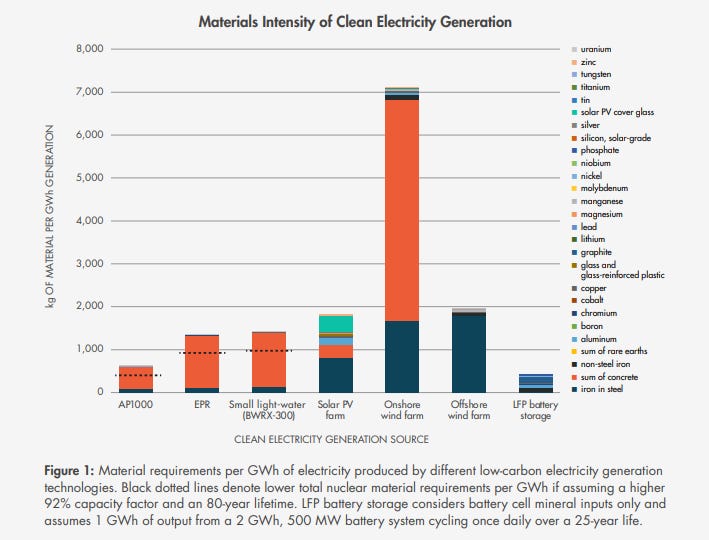
Energy is a hybrid world of inputs in order to sustain the current standards of modern life and while new alternative energies will be required to continue this demand growth, it’s hard to see how current inputs such as natural gas can be eliminated at a faster pace than the alternatives that are being deployed can come online.
‘and never mind that if the whole world decided to go electric tomorrow, we don’t have the transmission lines to get the electricity to the cities. It would take 30 years if we started tomorrow’
Electrical power transmission lines mapped out by the EIA, the U.S. electric transmission network consists of about 700,000 circuit miles.
Power transmission infrastructure has emerged as a critical constraint in the global transition to renewable energy and electrification. For every terawatt-hour (TWh) of annual electricity demand worldwide, approximately 170.88 miles (275 km) of transmission lines and 2,485 miles (4,000 km) of distribution lines are required.
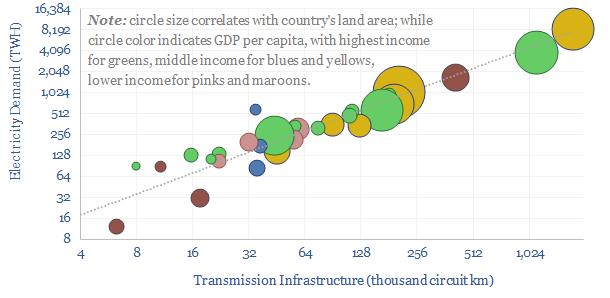
Every gigawatt (GW) of newly installed utility-scale renewable energy capacity typically requires about 500 kilometers of new or upgraded transmission lines, along with 8,000 kilometers of distribution infrastructure.
The U.S. alone has approximately 1,300 gigawatts (GW) of generation capacity. Meaning that if 500km of new or upgraded lines are needed for every 1GW currently installed, that would be 650,000 kilometers of transmission lines. To put this into perspective of the sheer size, this is enough transmission lines to wrap around Earth's equator about 16 times. The Department of Energy projects total wind capacity in 2050 at 404.25 GW across 48 states. While not all current lines would need to be upgraded, it’s important to understand the sheer size of the current grid in the U.S. and how difficult it will be to extrapolate true demand as technologies change.
‘Unfortunately for your grandkids we have a 120 year petroleum based infrastructure. Our whole lives depend on it’
Currently the bulk of electric generation still comes from natural gas as 43.65% while wind accounts for less than 12%. Retirement of wind is low compared to that of natural gas as many pro-alliterative energy projects expect the decommissioning of natural gas plants to continue.

However, the Biden-Harris administration through the U.S. Department of Transporation recently announced nearly $200 Million to Replace Aging Gas Pipes and the Public Utility Commission of Texas (PUC) said in June of this year that power developers in the state submitted 125 formal applications under the Texas Energy Fund (TEF) for the development of almost 56 gigawatts of new natural gas power generation in the coming years according to Forbes. This is off the backs of the Texas Legislature that appropriated $5 billion to fund the TEF for Fiscal Years 2025-2026. Below are current natural gas power plants in the United States.
According to Bloomberg’s New Energy Outlook (NEO) the energy transition scenario requires 46,000 terawatt-hours of power generation in 2050, nearly double today’s amount. The Net Zero Scenario, however, requires more than 80,000 terawatt-hours of generation, more than triple today’s amount.
A large portion of this demand will come in unrealized potential of Artificial Intelligence (AI) and the Large Language models (LLM) being fed. These monsters are extremely hungry for new energy not currently available on the grid to meet the demand needs.
‘You know what the kicker is? We are gonna run out of it before we find its replacement… The thing that’s gonna kill us all is running out before we find an alternative… Getting oil out of the ground is the most dangerous job in the world. We don’t do it because we like it. We do it because we run out of options… There ain’t nobody to blame but the demand that we keep pumping it.
Proved reserves of natural gas in the United States grew to a new record of 625.4 trillion cubic feet (Tcf) in 2021, a 32% increase year-over-year. While the world may be in the middle of an Energy Crisis due to low investment on supply versus the coming demands of the world that can only be met by all energy production, the amount of reserves in the ground aren’t the issue. It is the economics that matter when the prices of today’s produced barrels are lower than the breakeven of the costs to extract. The industry will find a way to get those barrels and gas out of the ground but the price necessary to incentivize that production will need to change.
Well thought out rant.
Loved this